Automotive
Understanding Internal and External Threaded Fasteners
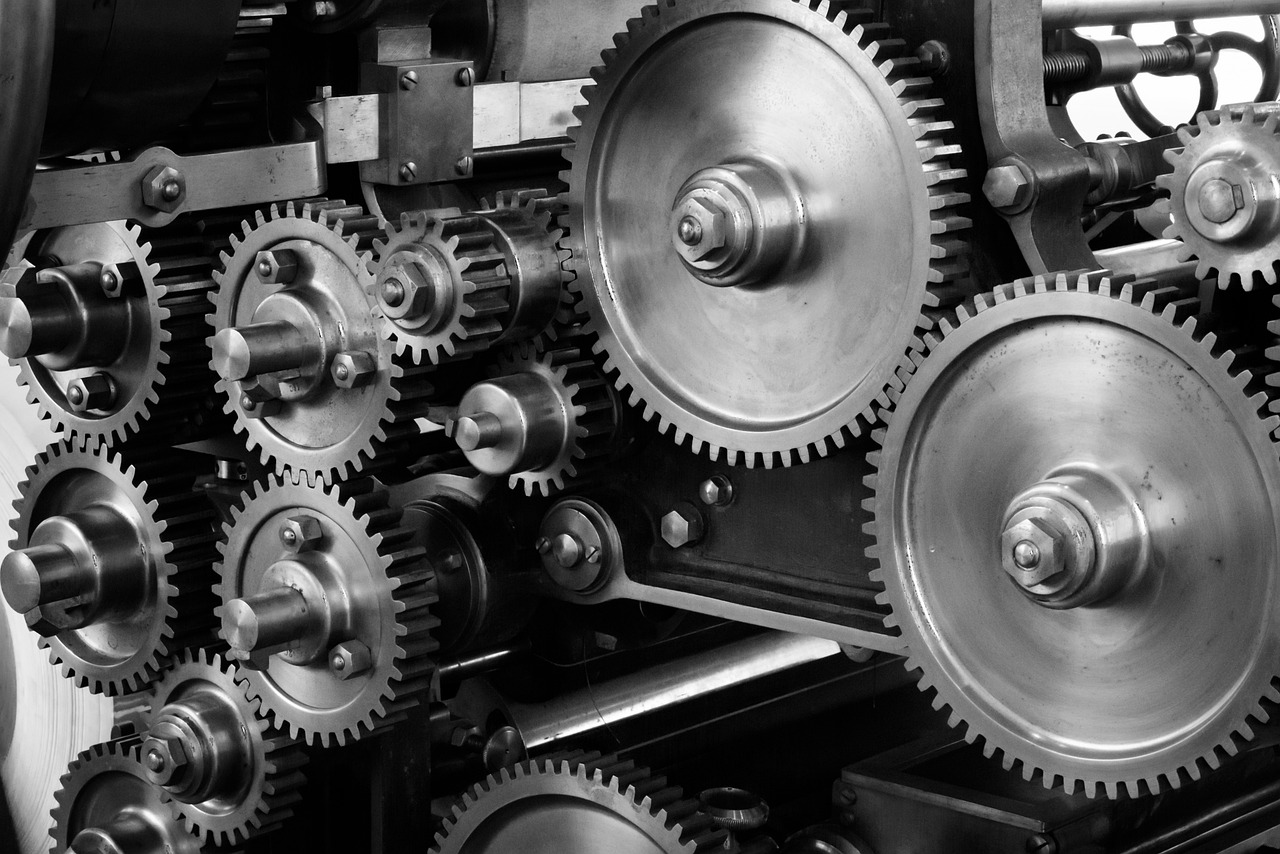
Threaded fasteners are essential components in mechanical assemblies, ensuring strong and reliable connections across various industries. From automotive to aerospace, these small yet crucial components provide the necessary grip and stability to keep structures intact. Whether you require internal threaded fasteners or external threaded fasteners, understanding their specific functions and applications is key to selecting the right fastener for your needs.
What Are Internal Threaded Fasteners?
Internal threaded fasteners, commonly known as nuts, feature a threaded interior designed to pair with externally threaded fasteners such as bolts and screws. These fasteners serve as the counterpart in fastening systems, creating a secure and stable joint that can withstand mechanical stress and vibrations. Their primary purpose is to provide a locking mechanism that holds two or more components together firmly.
The effectiveness of internal threaded fasteners depends on their design, material composition, and specific use cases. Hex nuts, for example, are widely used for general mechanical applications, while lock nuts include additional security features to prevent loosening due to movement or vibrations. Flange nuts, on the other hand, distribute pressure more evenly, reducing the likelihood of damage to the surfaces they secure. By selecting the appropriate type of nut, engineers and manufacturers ensure that mechanical connections remain intact even under high-stress conditions.
Applications of Internal Threaded Fasteners
Internal threaded fasteners play a critical role in various industries where durability and stability are paramount. In the automotive sector, they are essential in engine assemblies, chassis connections, and transmission systems. Their ability to distribute loads evenly makes them a preferred choice in structural engineering, where they reinforce buildings, bridges, and heavy machinery. Additionally, these fasteners are commonly found in electronic enclosures, providing the necessary grip to secure delicate components without causing damage.
Beyond industrial applications, internal threaded fasteners are frequently used in everyday objects, including furniture, appliances, and consumer electronics. Their versatility allows them to function across a broad spectrum of environments, making them indispensable in both large-scale manufacturing and household projects.
What Are External Threaded Fasteners?
External threaded fasteners, such as bolts and screws, feature threads on their outer surface, allowing them to be inserted into corresponding internal threads or directly into pre-tapped holes. Unlike internal threaded fasteners, which rely on a counterpart to create a secure connection, external threaded fasteners can often function independently, making them a more versatile choice for assembly applications.
The primary purpose of external threaded fasteners is to provide a strong mechanical grip that holds materials together. Their design varies depending on the intended use, with factors such as thread pitch, length, and head shape influencing their effectiveness. Bolts are typically used in high-load applications, often paired with nuts to create a firm joint. Screws, on the other hand, are more adaptable and can be used with or without nuts, making them ideal for securing components in a wide range of environments.
Applications of External Threaded Fasteners
External threaded fasteners are essential in construction, automotive manufacturing, and industrial machinery. In the automotive industry, bolts and screws are used to assemble everything from body panels to suspension systems, ensuring that vehicles remain structurally sound. Their presence in construction projects is equally significant, where they provide the necessary support for steel frameworks, bridges, and high-rise buildings.
In addition to industrial use, external threaded fasteners are found in household applications such as furniture assembly, appliance installation, and DIY projects. Their reliability and ease of use make them an ideal choice for both professional and amateur builders looking for durable and effective fastening solutions.
Key Differences Between Internal and External Threaded Fasteners
While both internal and external threaded fasteners serve the fundamental purpose of securing components, they differ in terms of design, function, and application. Internal threaded fasteners rely on external counterparts to complete a connection, whereas external threaded fasteners can often function independently. Additionally, the selection of materials varies depending on factors such as load-bearing requirements, environmental exposure, and durability expectations.
Material selection plays a crucial role in determining the strength and longevity of a fastener. Stainless steel fasteners, for example, offer excellent corrosion resistance, making them suitable for outdoor applications. Titanium fasteners provide high strength with minimal weight, making them a preferred choice in aerospace engineering. Carbon steel fasteners, known for their affordability and robustness, are commonly used in industrial applications where strength is a priority.
Choosing the Right Fastener for Your Needs
Selecting the appropriate fastener depends on various factors, including load capacity, material compatibility, and environmental conditions. For applications that require high durability, stainless steel or titanium fasteners may be the best choice, while standard steel fasteners provide an economical yet effective solution for general use. Understanding the specific requirements of your project ensures that you select a fastening solution that meets both performance and longevity expectations.
Another important consideration is thread type. Coarse threads provide better resistance to stripping and are easier to assemble, making them ideal for applications that involve frequent disassembly. Fine threads, on the other hand, offer a higher tensile strength and are better suited for high-precision applications.
Installation Best Practices
Ensuring the proper installation of threaded fasteners is crucial for achieving optimal performance. Applying the correct torque prevents both over-tightening, which can lead to fastener failure, and under-tightening, which may cause loosening over time. Using thread-locking compounds can further enhance stability by reducing the risk of loosening due to vibration.
Additionally, choosing the right tools for installation, such as torque wrenches and thread gauges, helps maintain consistency and accuracy. Regular inspections and maintenance of fasteners, especially in high-stress environments, contribute to long-term reliability and safety.
In a nutshell
Threaded fasteners, whether internal or external, are fundamental components in mechanical, structural, and industrial applications. Their ability to provide secure and stable connections ensures that machinery, vehicles, and buildings maintain their integrity under various conditions. By understanding the differences between internal and external threaded fasteners and selecting the appropriate type for each application, engineers and manufacturers can enhance the strength, reliability, and durability of their assemblies.
To explore a wide range of high-quality fasteners, visit Facil’s internal threaded fasteners and external threaded fasteners pages for more details on available products.
Explore TodayFirstMagazine and be the first to know current news updates to stay caught up.
